Bellway Homes’ ambitious experimental Plot 256 is a 2024 Building Awards finalist. Together with partners like MiTek, Bellway is implementing next-generation designs on today’s sites.
The UK construction industry moves at such a pace now that change is measured in years, not decades. The shift towards emphasising environmental stewardship and carbon efficiency has been rapid, and Bellway Homes has played a pivotal role.
The Bellway team lead by example. Their strategic goal, which is centred around its ‘Better with Bellway’ sustainability strategy, putting people and the planet first, includes:
- 46% lower Scope 1 and 2 carbon emissions by 2030
- 55% lower Scope 3 carbon emissions by 2030
- A 100% electric fleet by 2025
Achieving these ambitions means transforming architectural vision into actionable design. Even the most standard of tomorrow’s homes will incorporate large quantities of advanced tech. How will it all fit?
The Future Homes Standard (FHS) will doubtless increase this complexity, demanding technologies like MVHR systems and air source heat pumps. But until the FHS completes its slow drift to implementation, Bellway is seizing the initiative.
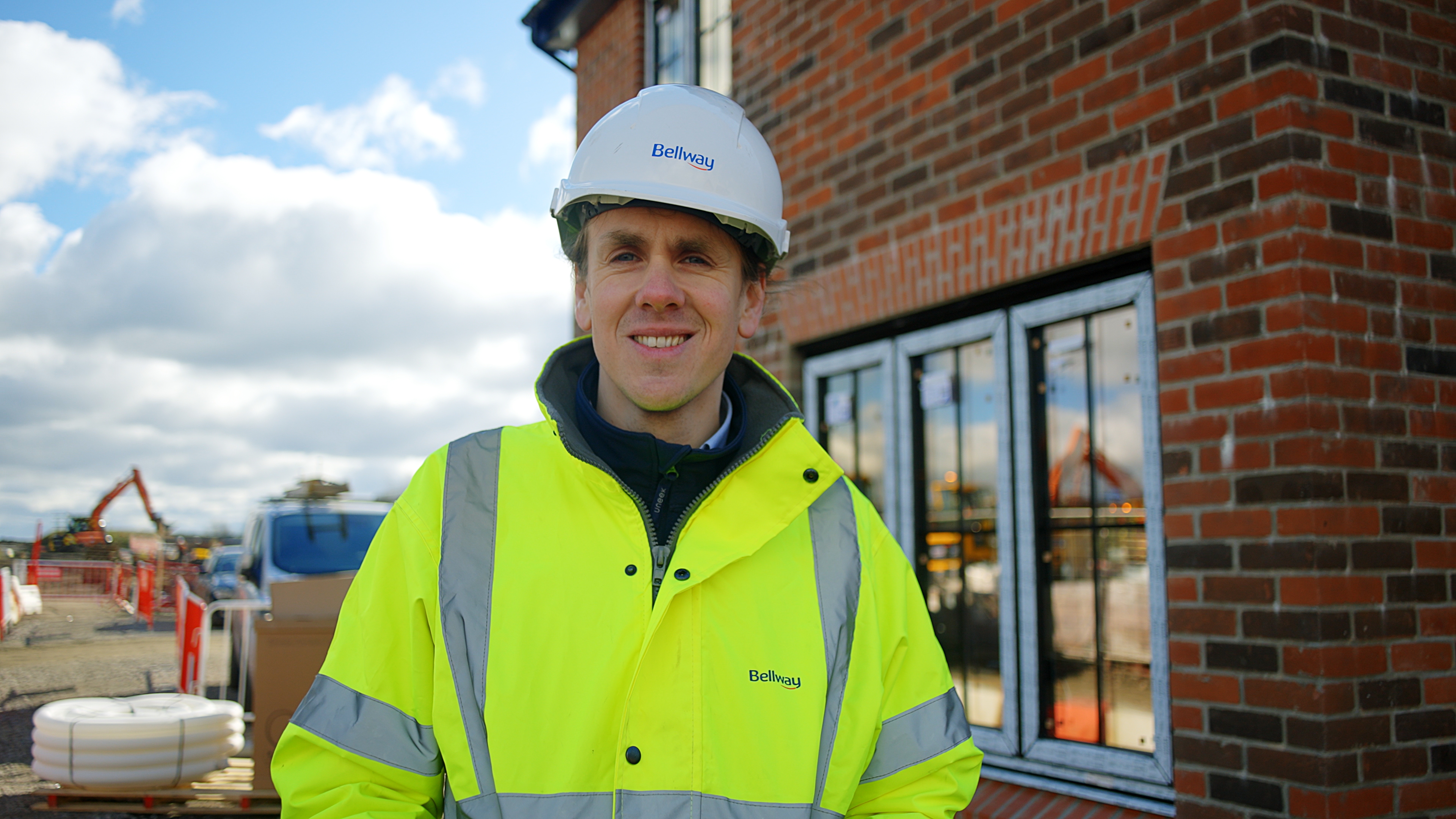
Taking cutting-edge technology from lab to the site
We spoke to David Arkley, Bellway’s Senior Architectural Technician, to learn more about how they show leadership on housing standards. It’s a long-running process, with one project building steadily on from the one before.
2023 saw Bellway collaborate with the University of Salford on The Future Home at Energy House 2.0. A state-of-the-art home was built inside a giant artificial weather chamber, to measure the performance of Bellway homes to test the impact of the latest sustainability technology, using climate models.
The Future Home produced compelling data to support technologies which might find their way into the finished FHS. But it’s outside the lab, in live field testing on real development sites, where Bellway are really shining right now.
They have partnered with Octopus Energy to create ‘Zero-Bills’ homes. These properties contain enough sustainable technology to save occupants over £1,800 per year in energy costs, with a guarantee of no energy bills for at least five years.
David and his team, along with the Manchester division, also contributed to Bellway’s experimental Plot 256 at their Barton Quarter development. It’s part of the Rivington Chase regeneration project, which will see £200 million invested in the creation of 1,600 homes. Here, Bellway set aside four test homes to trial different technologies from The Future Home, on a live building site.
Plot 256 gave the team free rein to envision, design, and build homes which will satisfy or surpass the final FHS. The goal was to learn vital lessons in actually implementing advanced technology at speed and scale.
For David’s team, the most exciting part was starting totally from scratch. As he puts it, “Plot 256 has the same footprint as our Scrivener House type, but that is the only similarity. The entire internal layout had to be remodelled.
“The challenge was the space we had; Integrating MVHR and other technologies into a regular-sized house of 1,200 square feet. But we got to see how everything fits together on site, how everyone comes together to actually deploy all this stuff.
“What it’s really done is push us to the forefront of what we can achieve, together with supply chain partners like MiTek and Zehnder. We’ve accomplished the end goal, or perhaps the spirit of the FHS; better built environments, better energy efficiency, better air quality. We’re a cut above in terms of pushing boundaries. It’s all still ongoing, but we now know it’s all achievable in practice as well as theory.”
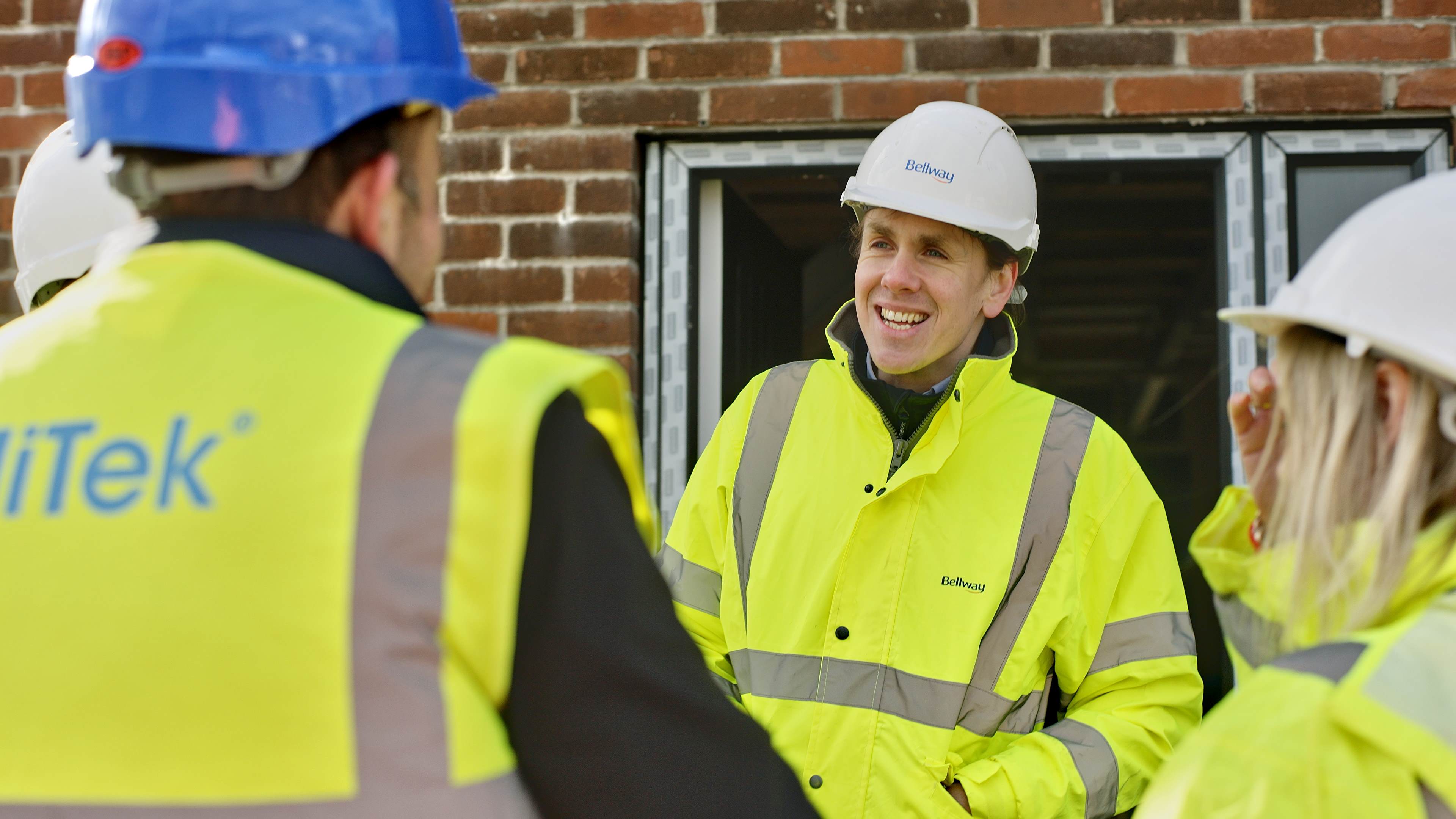
How is MiTek helping Bellway keep the standard high?
Success at Plot 256 involved integrating new technologies into regular-sized homes, turning theoretical designs into practical, sustainable living spaces. Tools like MiTek’s PAMIR 3D design software are facilitating better planning and problem-solving, ensuring smoother implementation of complex designs.
To David: “Seeing plans in 3D makes my life easier, and it lets me spot issues before they get to site, which makes their lives easier. People can build around each other; if I spot there’s a duct going through a some steel webbing, it takes 15 minutes to pull up designs and talk through a solution.
“Plot 256 would have been a lot more difficult to achieve without this. It’s our preferred way of working now. Even if contractors send us models in 2D, they get converted straight into our 3D BIM model.”
Then there’s the actual build process itself. Posi-Joist has quickly become the joist of choice for builders looking ahead to the FHS’ possible implications. Bellway is no different.
Open-web design means plenty of space for all that ducting, wiring, and plumbing. That make trades’ lives easier by helping them work around each other’s input. It means less drilling, less sawdust, cleaner, safer sites, and enormous time savings.
As David sees it: “Without Posi-Joist, these kinds of jobs can be done but it’s more difficult for everybody. I’d certainly hope we’ll use them on all our houses going forward. The time savings are important.
“For me at the design phase, they must save about a day in total. There’s no going back and forward if something’s not quite right; there’s flexibility on site to keep going. And when you’re building, compared to a solid joist where spacing holes is so important to keeping the structure strong, Posi-Joist must save a good couple of days per house during the build. And if you look at a development like Barton Quarter, 200-something homes, those benefits scale.”
Bellway’s leadership in sustainability is paving the way for a zero-carbon ready housing industry, where green communities can flourish. They’re showcasing how ambitious goals are achievable in the real world.
We’re proud to support the people who are taking these big steps forward for our industry.